Understand UKCA and apply it correctly to your products
The UKCA applies to all goods sold in England, Scotland and Wales. For goods that require CE labelling in the EU, the UKCA mark is usually also required in the UK. The "Authorised Representative" required for this must be based in the United Kingdom.
The experts at easyCE will be happy to help you place your products on the market and assess special cases. We are happy to support you with CE, UKCA and other marking.
Declaration of conformity done!
Receive your CE declaration of conformity ready for signature.
Risk assessment completed!
CE mandatory risk analysis conducted.
Relevant directives & standards applied!
Your product evaluated against relevant directives and standards.
Technical documentation created!
Receive a pragmatic, user-friendly operating manual.
CE mark attached!
Simply affix the CE mark and you're done.
FAQ
What is UKCA?
The UK left the European Union (EU) single market and the customs union on 31 December 2020. This means that the rules and regulations governing the sale of goods on the EU market no longer apply in the UK.
This market is now regulated by the UK, which has introduced its own regulatory system. It is called the United Kingdom Conformity Assessment or UKCA, and the primary legislation is "The Product Safety and Metrology etc. (Amendment etc.) (EU Exit) Regulations 2019".
Where does the UKCA apply?
The UKCA applies to all goods sold in England, Scotland and Wales. The situation in Northern Ireland (also part of the UK) is in transition as the "trade border" runs along a line in the Irish Sea between England and Ireland. In order to market goods in Northern Ireland, both a UKNI mark and the EU CE mark must be obtained and affixed.
When does the UKCA apply?
UKCA came into force on 1 January 2021. However, most goods on the UK market can make use of the transitional period for UKCA. This was last due to end on 31 December 2024 after being extended several times, but has now been suspended indefinitely. For manufacturers, this means that goods can only be sold in the UK with the CE mark until further notice.
For which goods does the UKCA mark apply?
Goods that require CE labelling in the EU generally require the UKCA mark
- machinery
- low voltage electrical equipment
- measuring devices
- elevators
- radio equipment
- personal protective equipment
- toys
- recreational craft and personal watercraft
- non-automatic weighing instruments
Which products with UKCA marking are subject to special rules?
The list consists of the following products:
- Medical devices and in-vitro diagnostics: Require registration with the UK Medicines and Healthcare products Regulatory Agency (MHRA). Specific classifications for devices and diagnostics, based on risk, with specific requirements. Requires a UK-based representative with appropriate authorisation.
- Rail interoperability Specifications and rules governing operation and construction to ensure the safety of cross-border rail operations.
- Construction products The UK Construction Product Regulations establish certain standards and harmonised testing requirements for certain construction products. The regulations set out five different "systems" for manufacturers to comply with in order to obtain the UKCA mark for a product.
- Civilian explosives The UK has essentially adopted EU rules and requirements for civilian explosives. However, the main change is the requirement for a UK-registered representative with comprehensive powers, as well as the registration and authorisation of the product with the competent local authorities.
What is required for UKCA marking?
The requirements for the use of the UKCA mark largely correspond to those for the CE marking in the EU. The differences depend on the product and must be researched for each product. The basic differences between the CE mark and the UKCA mark are as follows:
The importer must be a resident of the United Kingdom. Professional representatives established in the EU before 31 December 2020 will continue to be recognised, but newly established professional representatives must be established in the UK.
In the UK, what was previously referred to as a notified body is referred to as an authorised body and requires authorisation in the UK. Their function will be essentially the same: they will be commissioned by the importer or manufacturer to support and regulate the UKCA labeling process. Similarly, in the UK, "harmonised standards" are referred to as "designated standards". In many cases they remain very similar, but should be carefully checked for each product.
(EU companies importing products manufactured in the UK become "importers" in the EU and are subject to additional requirements).
The conformity assessment procedure for obtaining the authorisation to use the UKCA mark is very similar to the procedure used in the EU to obtain the CE mark. However, the details of the procedure differ for certain products and must be carefully examined.
How is the conformity of a product demonstrated?
A product must go through one of the conformity assessment procedures that the manufacturer selects from the procedures for the category into which it is classified. The manufacturer can also choose a procedure for a higher category, if available, the class should be set for each product.
A product may require either a self-assessment or the involvement of an approved body. The directive classifies products into different categories. These range from I to IV, according to the ascending order of the danger levels.
The use of an approved body is mandatory for products of category II or higher.
For Category II, III and IV products, the operating procedures and personnel shall be authorised by a competent third party in which the manufacturer, at the manufacturer’s discretion, recognised itself as an authorised body or an authorised body by the UK supervisory authority third-party organization can act.
In order to grant such approvals, the approved body or third party shall have carried out or verified the tests and tests or equivalent tests and tests specified in the relevant notified standards.
Where deemed appropriate due to the risks of the product, the manufacturer should sample the product examine its characteristics and risks and, if necessary, maintain a list of complaints about non-compliant products and recalls of such products. The manufacturer shall inform the dealers of this monitoring.
What is the experimental design method?
The design of a product may be fully or partially validated by an appropriate test program performed on a sample representative of the product or category.
The test programme shall be clearly defined before the test and accepted by the approved body responsible for the design conformity assessment module (if any). This programme shall lay down the test conditions and the criteria for acceptance or rejection. The actual values of the essential dimensions and characteristics of the materials that make up the tested product must be measured before testing. Where appropriate, the critical areas of the product must be observed during testing with appropriate equipment capable of detecting loads and stresses with sufficient accuracy.
What role does the accredited body play in the assessment and examination?
In certain conformity assessment procedures, it should be possible for each part to be inspected and tested by an approved body or user inspector as part of the final evaluation of the product. In other cases, arrangements should be made to ensure that the final assessment can be monitored by the approved body through unannounced visits.
The manufacturer shall provide the approved body with access to the manufacturing, acceptance, testing and storage facilities and provide it with all the necessary documentation, including the quality assurance system, technical documentation and quality reports such as test reports, test data, calibration data, reports on the qualifications of employees in this area, etc.
The accredited body shall conduct regular audits to ensure that the manufacturer maintains and applies the quality assurance system and shall provide it with an audit report. The minimum frequency of regular audits is a complete reassessment every three years.
In addition, the approved body may make unannounced visits to the manufacturer. The need and frequency of additional visits shall be determined on the basis of a visit control system operated by the approved body. The visit control system should take into account in particular the following factors: the product category, the results of previous monitoring visits, the need for corrective action, where appropriate, specific conditions relating to the approval of the system and significant changes in the organisation of production, production processes or methods. During these visits, the approved body may carry out product tests to verify the proper functioning of the quality assurance system. The accredited body shall provide the manufacturer with a report of the visit and, if tests have been carried out, a test report.
What technical documentation is required?
The technical documentation for creating an UKCA label depends on the specific legislation for the product. However, all documents must be written in English.
In general, they contain records of how the product was designed and manufactured, how it has been proven that the product meets the relevant requirements, as well as the addresses of the manufacturer and all storage facilities. These documents are essentially the same as those used for CE marking in the EU. However, a careful review of the UK requirements for each product should be made and additional documentation should be provided where possible. The documents shall be kept for at least ten years and shall be easily accessible at the request of an enforcement authority.
What must the declaration of conformity contain?
For many products, a UK declaration of conformity is required, which essentially corresponds to that required by the EU. In general, the declaration would state that the product complies with the legal requirements applicable to the product in question, and it would contain the following information
- the name and full business address of the manufacturer or representative authorised to issue the declaration in the UK
- a type of identification number, which can be the serial number, product or batch number, model or type,
- a statement stating that it is issued under the sole responsibility of the manufacturer
- a description of the product and the conformity assessment procedure used.
- a declaration that the declaration complies with the relevant legislation on designated standards
- references to the relevant designated standards used in or referred to in the technical specifications
- the name, address and identification number of the accredited body that carried out the conformity assessment procedure
- the identity and signature of the authorised person, and
- the date of issue of the declaration.
We at easyCE provide the instructions for explaining the specific product.
Pharmaceutical and life sciences products should be carefully considered as the UKFC regulations contain many specific requirements for them.
After all the necessary steps have been taken to ensure conformity, the UKCA mark should be applied to the product.
How is the UKCF mark applied?
Upon receipt of approval, the UKCA mark must be affixed to each product. If the product does not allow the marking directly, the marking should be made on the packaging and related documents.
The minimum requirements for marking are: the letters remain proportional even when reduced or enlarged, they are at least 5 mm high and clearly visible, readable and indelible printed.
This is the standard format:
Get CE-marking done in 3 simple steps
Step 1
Request expert opinion
Ask for our expert opinion free of charge and find out what is necessary for the CE marking of your product. Be prepared to describe your product in broad terms.
Step 2
Receive our offer
If your product is subject to CE marking, we offer you our support with the CE marking and all accompanying measures. We will be happy to explain necessary steps on the phone.
Step 3
We get it done
When you place an order, you will be assigned your own personal CE expert who will carry out your CE marking and accompany you throughout the entire process. Your expert will also be at your side after the CE marking has been successfully completed.
Get CE-marking done, worry-free
Trust the experts of product safety and conformity
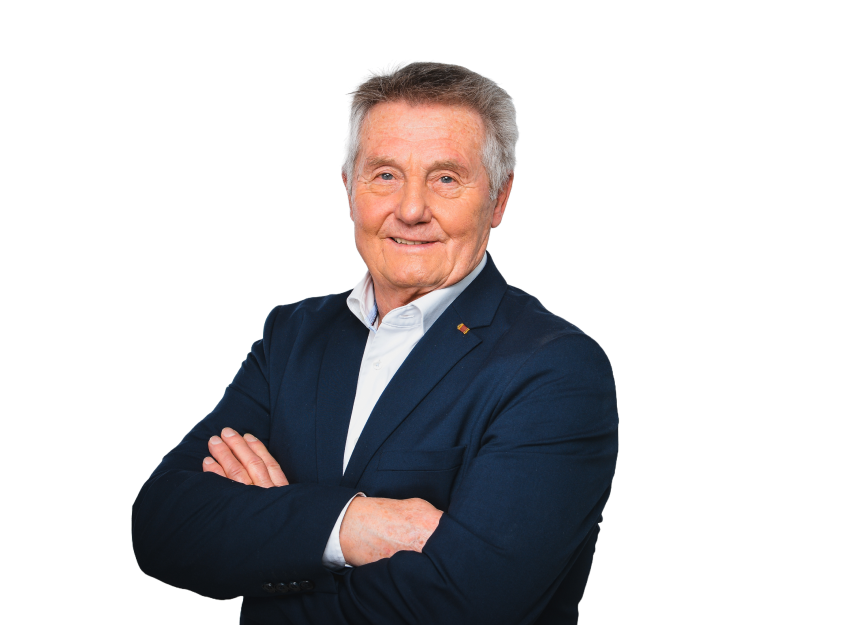
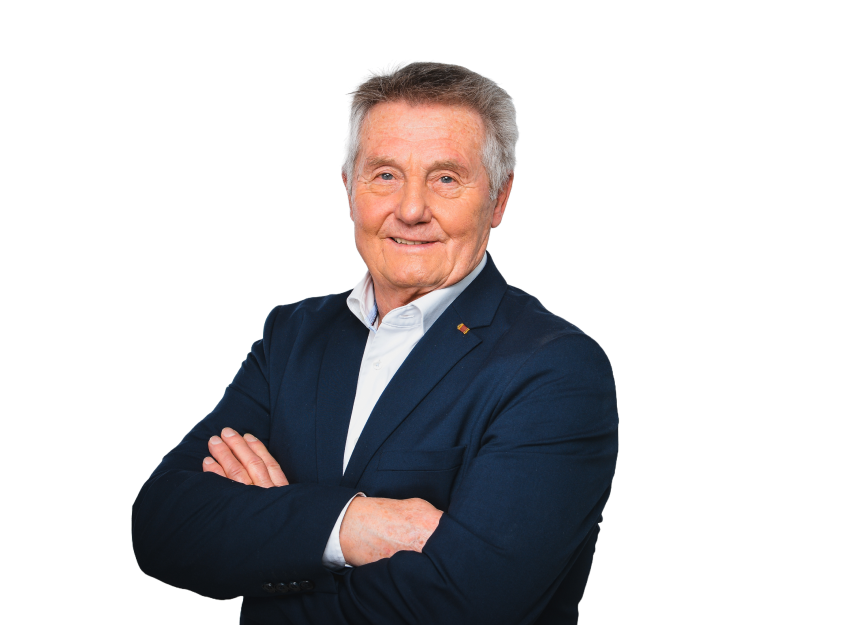
Willy Lebherz - Founder and Managing Director of easyCE
- Expert in product safety and conformity since 1995
- Recipient of the "Medal of the Order of Merit of the Federal Republic of Germany", awarded in 1983 by the then Federal President Carl Carstens
- Master of measurement and control technology
- Captain (ret.), Project Officer for Technical Logistics in the Army Material Office and Chief of the Telecommunications Repair Company
easyCE is a digital, dynamic engineering office with a focus on product safety and product conformity - especially CE-marking. We support manufacturers, operators and dealers in designing products safely and offering them on the market in compliance. We are a "full-service provider" and can take over the entire conformity assessment process for you if you wish. To do this, we support you in carrying out risk assessments, researching standards, product analyses, developing suitable safety precautions, preparing user-friendly technical documentation, coordinating tests and all other accompanying measures. easyCE was founded in southern Germany, but is now active globally.
We know what you need to do to get CE-marking done, worry-free.